
DISCOVER KENOTEQ
It all starts with a better brick…
OUR MISSION
Kenoteq is innovative and ambitious, aiming to become a global leader in the world of ultra-low carbon sustainable building materials, whilst providing local circular waste solutions which support local supply chains and drive down carbon emissions.
THE PROBLEM
The world’s finite resources are being rapidly depleted.
More than a third of waste in global landfill is estimated to be of demolition and construction origin.
There is a distinct lack of low carbon materials to meet net zero carbon targets, and a fundamental need for sustainable building materials.
Produce low carbon building materials made from near 100% recycled content.
Repurpose waste to instigate and sustain circular economy practices.
Provide high-performing materials to contribute towards net zero carbon targets.
THE SOLUTION
Our unique, patented methodology
We're revolutionising traditional brick-making methods. Recycled materials, no waste, no firing, fast local production.
Our products are grounded in science: with over a decade of research, development and testing our fully circular, patented, low energy production process allows us to create our low carbon products to a patented proprietary formation.
Our fully circular process allows us to create our products fit for use within 24 hours of the processed waste arriving at our factory.
-
The K-BRIQ® and associated products are made from over 90% recycled aggregates from construction and demolition waste, including old bricks, rubble and mortars, which are screened, washed, processed and certified inert by our waste management partners.
We add recycled plasterboard to the aggregates together with inert recycled pigments, bringing our recycled material inputs to over 95%. -
Our own ‘secret sauce’ is added to our patented formulation. This proprietary non-toxic binder is the final vital ingredient.
-
The input streams are industrially mixed before being formed under high pressure.
-
Unlike traditional clay bricks, which require significant energy and resources for manufacturing and typically utilise extrusion technology, our method employs hydraulic compression technology at high pressure to shape the products. This production process consumes less than 10% of the energy used in traditional brick production.
-
The K-BRIQ® and associated products are unfired, eliminating a reliance on fossil fuels and high temperatures as in traditional brick production.
Following compression, the products are cured at very low temperatures for a short period within our drying chambers.
-
Kenoteq’s production process is very short compared to traditional brick production. It takes only 24 hours to manufacture and cure a K-BRIQ® from the processed waste arriving at our factory to it being ready for distribution.
THE RESULT
The world’s most sustainable building materials, offering the design and construction sector ultra-low carbon, sustainable building products and aesthetic architectural and interior surfaces, whilst also answering the sector’s waste issues.
OUR STORY
Born from a serendipitous meeting, Kenoteq emerged from a visionary idea during conversations on geo-environmental challenges in construction waste management between cross-disciplinary experts at Heriot Watt University in Edinburgh, UK and Scottish waste management specialist, Hamilton Waste & Recycling Ltd.
Fuelled by a scarcity of building supplies, legislative waste reduction demands, the need for truly sustainable building materials to help decarbonise the built environment and a surge in new housing construction mandated by the government, Kenoteq was spun-out of Heriot Watt University in 2019 as a registered company ready to progress final prototyping, product certification and raise investment capital to set up a commercial scale production facility and scalable business and production model. Kenoteq is grateful for the funding it received from Construction Scotland Innovation Centre (now BE-ST), Scottish Enterprise and Zero Waste Scotland’s Circular Economy Investment Fund, and is actively pursuing Series A funding.
With global economies setting net zero targets and beginning to mandate carbon reduction and waste recycling targets, the K‑BRIQ® stands as the most innovative and low carbon brick in the market, featuring a core commitment to sustainability through circular economy processes. Boasting the lowest embodied carbon of any commercially available bricks, as well as the highest recycled waste content, the K‑BRIQ® holds UK and US granted patents, with European and Canadian patents pending. The K-BRIQ is fully BBA certified in the UK (Agrement Certificate 25/7367) and certified in the USA through Qualtim. European certification is underway.
The company and product are recipients of prestigious awards including the BE-ST Circular Economy Award 2023, Dezeen Award 2022 in Sustainable Design, VIBES Scottish Environmental Business Awards 2022 – Circular Scotland, Sacyr iChallenge Awards 2022, and The Times Higher Award: STEM Research Project of the Year 2020.
Kenoteq is on a mission.
Our vision is to deliver certified bricks for exemplar projects, blazing a trail in the circular economy revolution and bringing a scalable manufacturing and sustainable product solution, together with waste management partners, into an international marketplace.
Meet our team
We are proud at Kenoteq to be supporting a local supply chain and creating new green jobs throughout our business. We look forward to creating new jobs within our company and its new regional production facilities as we expand across the UK and internationally.
-
Andrew Holt
CHIEF EXECUTIVE OFFICER
-
Dr. Sam Chapman
CO-FOUNDER & EXECUTIVE DIRECTOR
-
Prof. Gabriela Medero
CO-FOUNDER & NON-EXECUTIVE DIRECTOR
-
Lucy Black
HEAD OF BUSINESS DEVELOPMENT
-
Dr. Ilias Sofikitis
TEST ENGINEER
-
Shona Williamson
PRODUCT DEVELOPMENT ENGINEER
-
Keith Gillespie
PRODUCTION OPERATOR
-
Scott Gillespie
PRODUCTION OPERATOR
-
Paul Grant
PRODUCTION OPERATOR
-
‘A Circular Economy Approach’
Through recycling construction and demolition waste, Kenoteq is both diverting waste from landfill and reducing the reliance on the energy intensive and environment scarring extraction of new aggregates. We are also reducing the need to use high carbon clay and cement-based bricks in construction.
A Circular Economy approach ensures that materials are retained within productive use, in a high value state, for as long as possible. It is a move from the current linear ‘take, make, dispose’ model and focuses on reshaping business and economic systems so that waste is ‘designed out’ of how we live.
-
Our concept is a closed loop system finding an outlet for demolition wastes, creating a new building material that is 100% recyclable itself, all whilst significantly reducing carbon and contributing to net zero goals and ESG targets. A symbiotic relationship has been developed with the material banks, the waste processors demolition raw material, and the end-user developers and builders to reduce their carbon footprint.
The K-BRIQ® concept is particularly suited to demolition and regeneration projects, where waste from site can be recycled into new high value façade and decorative surfaces for re-use on the regenerated site. For large-scale regeneration projects, consideration at masterplanning stages can be given to setting up waste processing and K-BRIQ® production facilities on-site, building a local supply chain, creating local jobs and leaving a legacy employer as well as environmental benefits at the end of the project.
Frequently Asked Questions
-
Contact our sales team to discuss the requirements for your project. We would love to send you a sample fit for your project.
Request samples -
Kenoteq sells directly, we do not sell through distributors or merchants at the current time. Contact us to find out current lead times and to place an order.
Minimum Order Quantity - in the early stages of our business, we prioritise building a diverse portfolio of reference projects, irrespective of their size.
Therefore, we welcome discussions regarding smaller order quantities. Please do not hesitate to reach out to us to explore project requirements for orders under 5m2 (equivalent to 300 K-BRIQ®s). -
Our current product formulation uses over 96% of recycled materials. Our recycled input materials are processed by our waste management partners to strict standards overseen by the Environmental Protection Agencies.
Our products are made from certified inert recycled construction and demolition aggregates (old bricks, old rubble, old mortars etc), recycled plasterboard (gypsum) together with recycled pigments. Our goal is to produce products made from 100% recycled materials. -
Speak to us directly about any projects outside the UK so we can better understand your applications and any relevant certification requirements, together with shipping options and embodied carbon considerations. We aim to roll out international manufacturing and distribution operations over the next few years.
-
Yes our products are 100% recyclable and can be repurposed to make new products at the end of their life cycle.
-
The certified technical specification is listed on the product pages, together with a downloadable BBA Certificate. Contact us if you have further questions.
Installation guides are available on order and on request.
-
The K-BRIQ® is fully certified for the UK market (Agrement Certificate 25/7367), and for the US market through DrJ. allowing its certified use in exterior and interior environments. European certification is underway.
The K-SLIP™ can be used in interior applications and self-certified applications currently. The K-SLIP™, together with a façade fixing system, will commence certification shortly with a certified system product expected to be available in 2025.
Our Environmental Product Declaration (EPD) certificate and Design Guide will also be available later in 2025.
-
We have now delivered CPDs to nearly 3,000 specifiers and clients.
We host a monthly virtual CPD, open to everybody, bookable via Eventbrite
Or contact us if you would like to book a CPD hosted specifically for your organisation.
-
For larger scale projects, we can offer a bespoke development service for both colour and shape/size development. Please contact us to discuss your requirements.
-
Our ambition is to work collaboratively with you to evaluate the suitability of on-site waste for recycling into K-BRIQ®s or related products. Depending on the demolition site's location, we may engage local regulated waste partners to handle and transport the waste to the nearest Kenoteq factory.
We will work closely with regeneration sites in their masterplanning to ascertain the suitability for K-BRIQ®s factories to be established on-site to convert the regeneration site waste into façade and interior surface products for re-use in the new builds on the site.
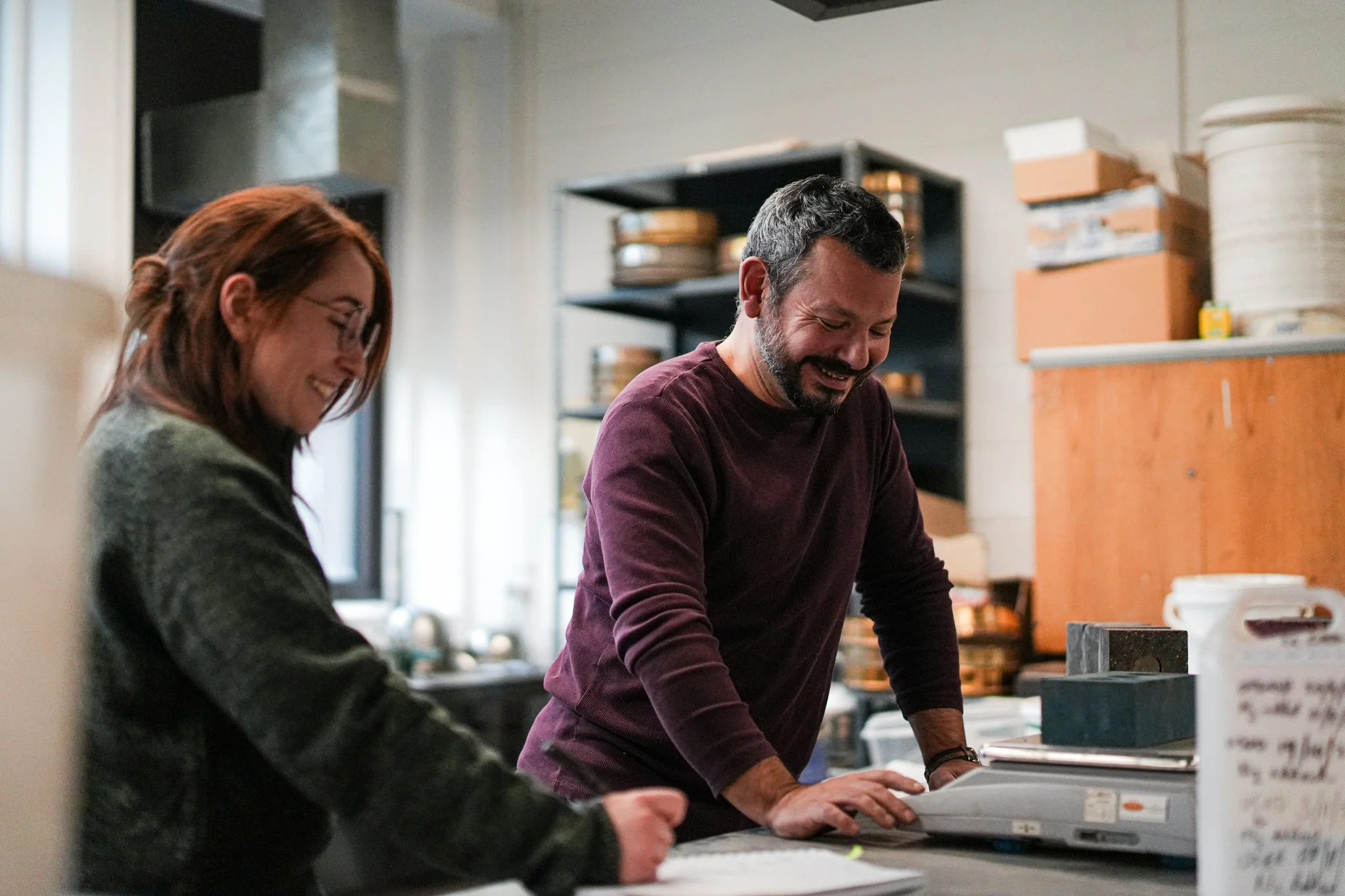